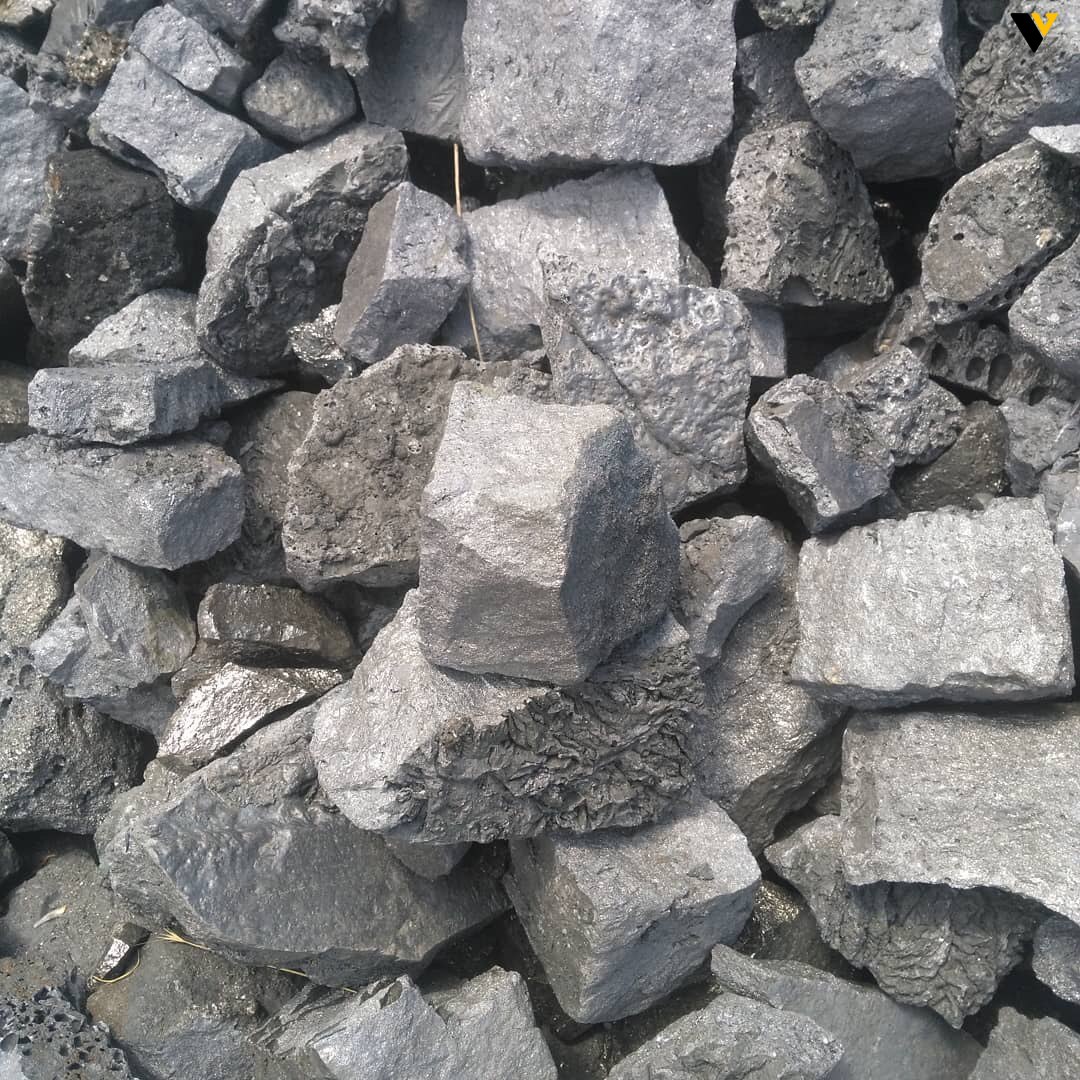
FERROSILICON
مراحل تولید فروسیلیس: یک فرآیند پیشرفته
فروسیلیس، آلیاژی حیاتی از آهن و سیلیسیم، بهعنوان یکی از کلیدیترین مواد در صنایع متالورژی، فولادسازی و ریختهگری شناخته میشود.
این ماده با خواص منحصربهفرد مانند مقاومت در برابر خوردگی، اکسیژنزدایی و بهبود خواص مکانیکی آلیاژها، نقش مهمی در تولید محصولات باکیفیت ایفا میکند.
در این مقاله جامع، مراحل تولید فروسیلیس بهصورت پیشرفته بررسی میشود، همراه با جزئیات فنی، جداول اطلاعاتی، سوالات متداول، چالشها، فرصتها و نتیجهگیری. 🚀
فروسیلیس چیست و چرا اهمیت دارد؟
فروسیلیس (Ferrosilicon) آلیاژی است که از ترکیب آهن و سیلیسیم با درصد سیلیسیم بین ۱۵ تا ۹۰ درصد تشکیل شده و ممکن است حاوی مقادیر ناچیزی از عناصری مانند آلومینیوم، کربن، گوگرد، فسفر یا منگنز باشد.
این ماده به دلیل ویژگیهای متالورژیکی خاص، در صنایع مختلفی از جمله فولادسازی، ریختهگری، تولید منیزیم و حتی صنایع الکتریکی (مانند تولید فولادهای مغناطیسی) کاربرد دارد.
رنگ فروسیلیس معمولاً خاکستری نقرهای بوده و نقطه ذوب آن بین ۱۲۹۰ تا ۱۳۹۰ درجه سانتیگراد است.
❓در این بخش چندین ویژگی کلیدی فروسیلیسم را باهم بررسی میکنیم:
اکسیژنزدایی قوی:
حذف اکسیژن از مذاب فولاد، کاهش تخلخل و بهبود کیفیت محصول.
افزایش استحکام و سختی:
بهبود خواص مکانیکی فولاد و چدن.
جوانهزایی در چدن:
ایجاد ساختار کریستالی مناسب در ریختهگری.
خواص مغناطیسی:
مناسب برای تولید هستههای ترانسفورماتورها و موتورهای الکتریکی.
مقاومت در برابر خوردگی:
افزایش دوام محصولات در محیطهای خورنده.
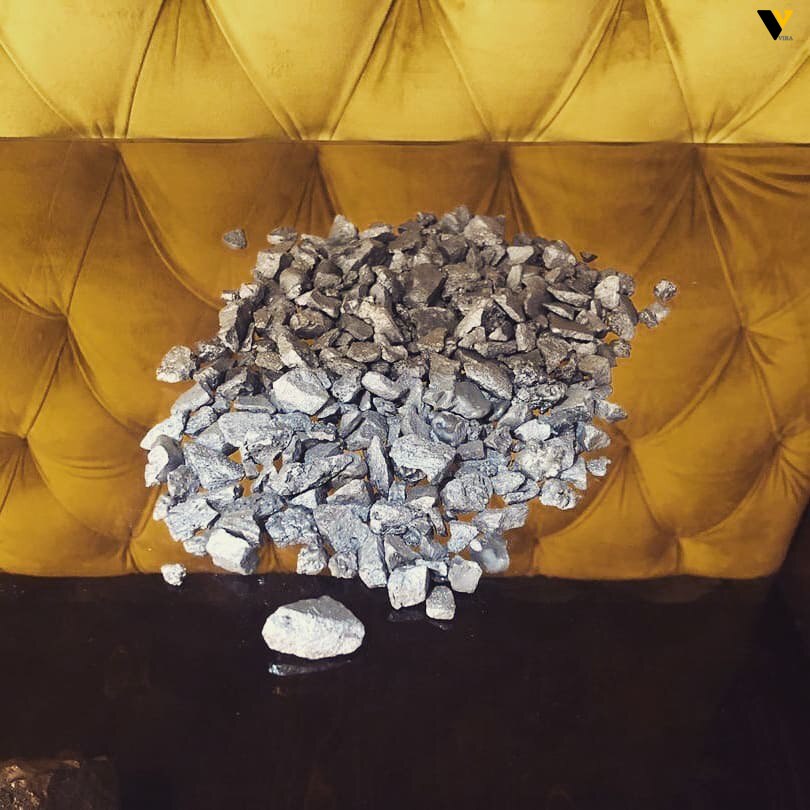
مواد اولیه و آمادهسازی: پایه تولید فروسیلیسیم
تولید فروسیلیس نیازمند مواد اولیه باکیفیت و فرآیند آمادهسازی دقیق است. مواد اولیه اصلی و نقش آنها به شرح زیر است:
1.سیلیس (کوارتز یا سیلیس آمورف): منبع اصلی سیلیسیم با خلوص ۹۶-۹۹٪ SiO₂. کیفیت سیلیس تأثیر مستقیمی بر خلوص محصول نهایی دارد.
2.اکسید آهن: بهصورت پوسته اکسیدی (Mill Scale)، سنگ آهن یا ضایعات آهنی تأمین میشود.
3.مواد احیاکننده: کک متالورژیکی، زغالسنگ یا زغالچوب برای تأمین کربن موردنیاز واکنشهای احیا.
4.مواد افزودنی: خمیر الکترود (برای بهبود هدایت الکتریکی)، خردهچوب (برای ایجاد تخلخل در شارژ) و گاهی فلاکسها برای کاهش دمای ذوب.
فرآیند آمادهسازی مواد اولیه فروسیلیکون:
فرآیند آمادهسازی مواد اولیه شامل جمعآوری، تمیز کردن،تبدیل مواد خام به حالتی مناسب برای تولید محصول نهایی است.
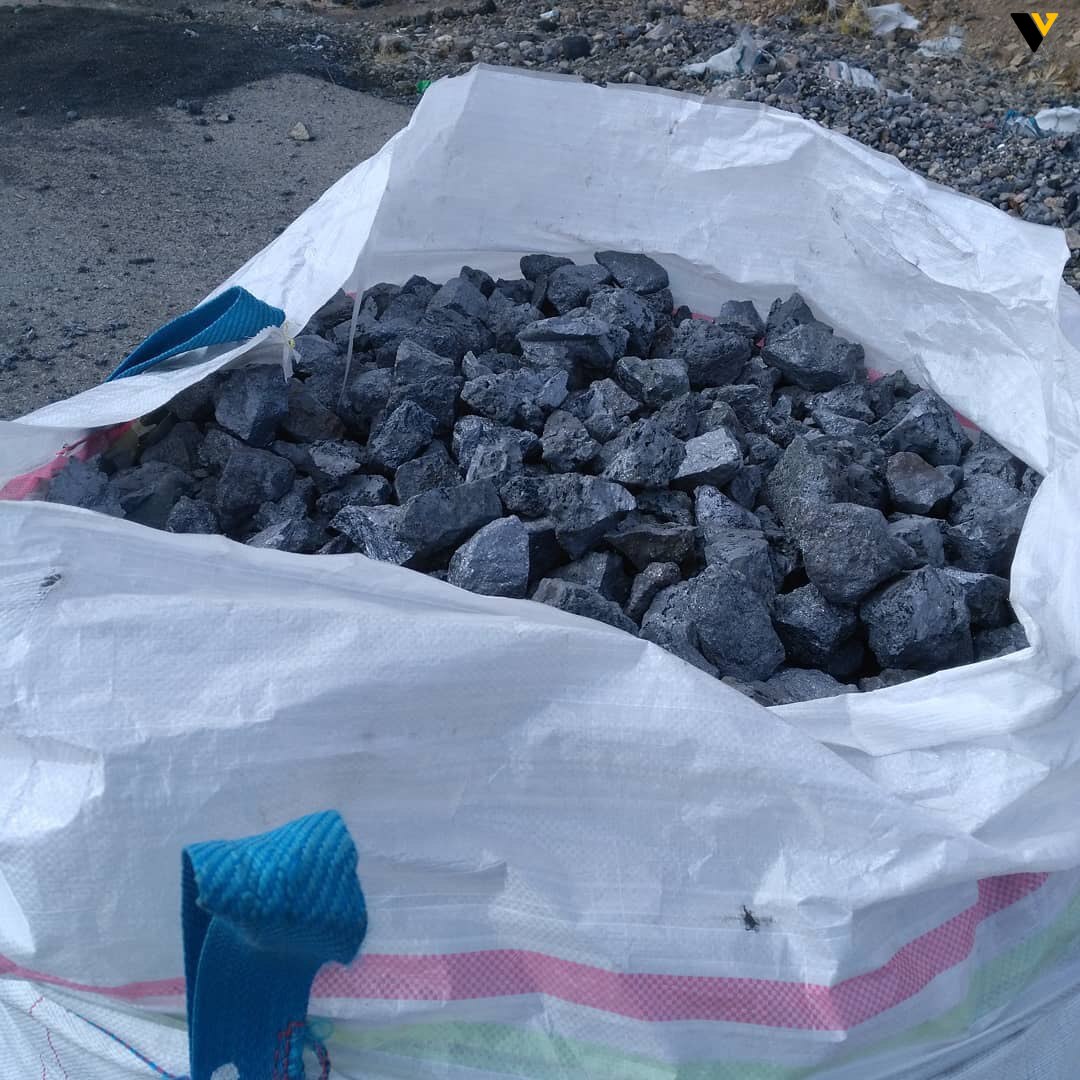
فرآیند تولید فروسیلیس: قلب تپنده صنعت
تولید فروسیلیس در کورههای قوس الکتریکی غوطهور (Submerged Electric Arc Furnace) انجام میشود که یکی از پیشرفتهترین تجهیزات صنعتی در متالورژی است.
این فرآیند به دلیل مصرف انرژی بالا و پیچیدگیهای شیمیایی، نیازمند تکنولوژیهای مدرن و کنترل دقیق است.
1. شارژ کوره
و فرآیند ذوب ⚡
مواد اولیه آمادهشده از طریق سیستمهای نوار نقاله یا قیفهای خودکار به داخل کوره شارژ میشوند.
کورههای قوس الکتریکی با جریان ۸۰-۱۲۰ کیلوآمپر و دمای ۲۰۰۰-۲۵۰۰ درجه سانتیگراد کار میکنند.
مراحل اصلی ذوب:
-
گرمایش اولیه: مواد اولیه در تماس با قوس الکتریکی گرم شده و به دمای واکنش میرسند.
-
واکنشهای شیمیایی: کربن موجود در کک، اکسید سیلیسیم (SiO₂) و اکسید آهن (FeO) را احیا کرده و سیلیسیم و آهن آزاد تولید میکند:
-
SiO₂ + ۲C → Si + ۲CO
-
FeO + C → Fe + CO
-
-
تشکیل فروسیلیس مذاب: سیلیسیم و آهن مذاب با یکدیگر ترکیب شده و در کف کوره جمع میشوند.
-
تولید غبار میکروسیلیکا: بخار سیلیسیم (SiO) در تماس با اکسیژن بهصورت ذرات ریز میکروسیلیکا (SiO₂) جامد شده و توسط سیستمهای فیلتراسیون جمعآوری میشود.
2. تخلیه
و خنکسازی 🧊
هر ۲ تا ۳ ساعت، فروسیلیس مذاب از طریق دریچههای کوره به پاتیلهای مقاوم در برابر حرارت منتقل میشود.
مذاب در قالبهای فلزی یا بسترهای ماسهای ریخته شده و طی چند ساعت سرد و جامد میشود.
دمای محیط خنکسازی باید کنترلشده باشد تا از ترکخوردگی محصول جلوگیری شود.
4. خردایش، دانهبندی
و غربالگری 📏
فروسیلیس جامد توسط سنگشکنهای فکی و مخروطی به قطعات کوچکتر خرد شده و سپس با سرندهای لرزشی به دانهبندیهای مختلف تفکیک میشود.
دانهبندیهای رایج شامل ۰-۳، ۳-۱۰، ۱۰-۶۰ و ۶۰-۱۵۰ میلیمتر است که هر یک کاربرد خاصی دارند.
5. بستهبندی
و عرضه 📦
فروسیلیس دانهبندیشده در کیسههای بزرگ (Big Bag) با ظرفیت ۱ تا ۲ تن یا بهصورت فله بستهبندی میشود.
محصول نهایی با استفاده از سیستمهای بارگیری خودکار به انبار یا مستقیماً به مشتریان ارسال میشود.
غبار میکروسیلیکا، محصول جانبی این فرآیند، نیز در کیسههای مخصوص بستهبندی شده و به صنایع سیمان و بتن فروخته میشود.
دانه بندی (میلیمتر) | نوع بستهبندی | کاربرد رایج |
---|---|---|
0–1 | کیسه 25 یا 50 کیلویی | صنایع شیمیایی، تولید پودر فروآلیاژ |
1–3 | کیسه جامبو یا فله | صنایع ریختهگری دقیق، فولادهای آلیاژی |
3–10 | فله یا کیسه جامبو | فولادسازی کوره قوس، چدنریزی |
10–60 | فله در واگن یا کامیون | صنایع بزرگ فولادسازی، احیای کربوترمال |
+60 | فله یا مخصوص سفارشی | استفادههای خاص صنعتی، جذب اکسیژن |
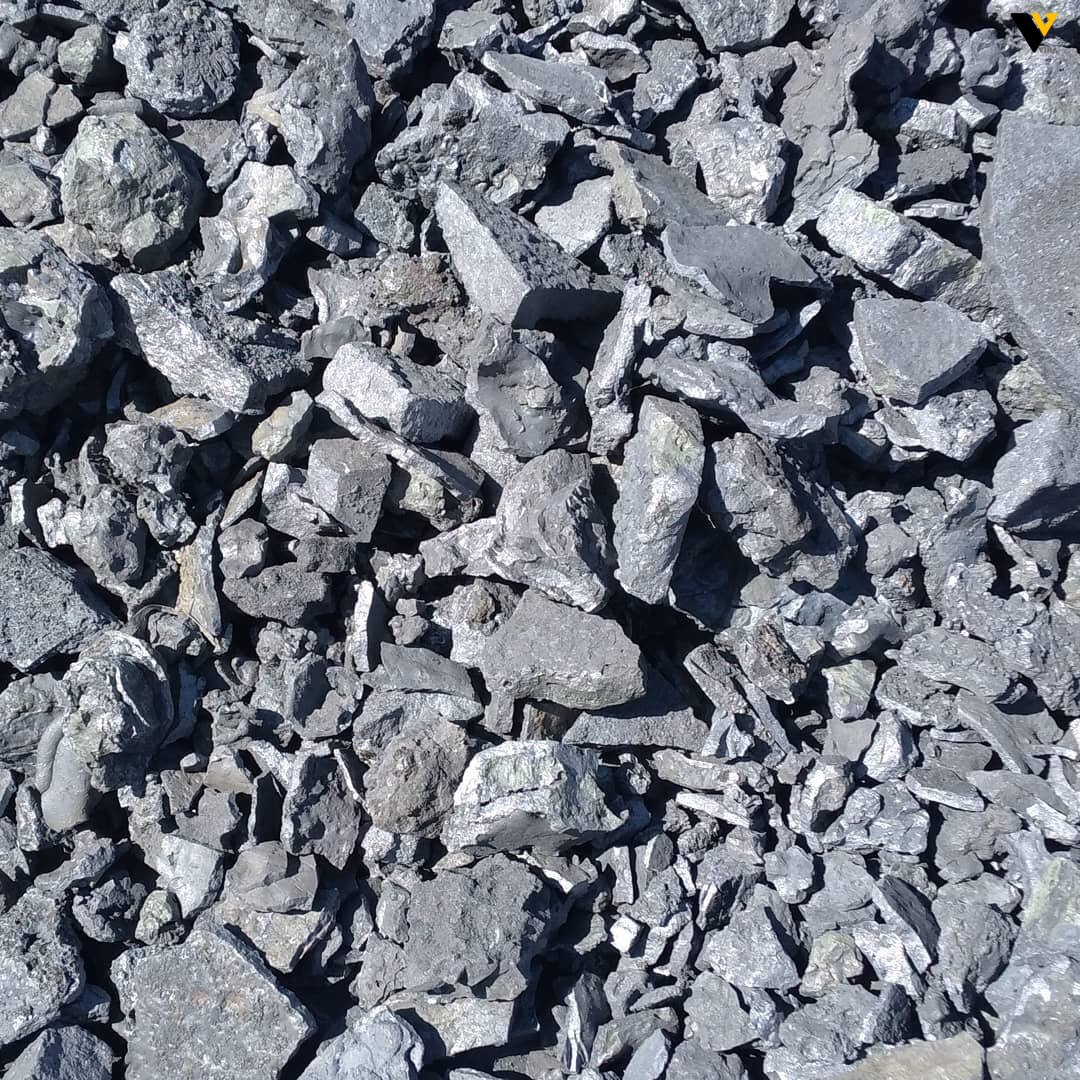
فناوریهای مدرن و نوآوریها در تولید فروسیلیس
صنعت تولید فروسیلیس با پیشرفتهای تکنولوژیکی به سطح جدیدی از کارایی و پایداری رسیده است. برخی از نوآوریهای کلیدی عبارتاند از:
1. اتوماسیون و دیجیتالسازی:
استفاده از سیستمهای PLC (Programmable Logic Controller) و نرمافزارهای SCADA برای کنترل دقیق شارژ، دما و جریان کوره.
2. بهینهسازی مصرف انرژی:
کورههای مدرن با الکترودهای گرافیتی و سیستمهای بازیافت حرارت، مصرف برق را تا ۲۰٪ کاهش دادهاند (میانگین مصرف: ۸۵۰۰-۱۲۰۰۰ کیلوواتساعت به ازای هر تن فروسیلیس).
3. مدیریت پسماند و بازیافت:
سیستمهای فیلتراسیون پیشرفته (مانند فیلترهای کیسهای) تا ۹۵٪ غبار میکروسیلیکا را جمعآوری کرده و بهعنوان محصول جانبی با ارزش افزوده عرضه میکنند.
4. کنترل کیفیت پیشرفته:
دستگاههای آنالیز طیفی (مانند XRF و ICP) برای بررسی لحظهای ترکیب شیمیایی محصول و اطمینان از انطباق با استانداردهای بینالمللی (مانند ISO 5445).
5. کاهش انتشار گازهای گلخانهای:
استفاده از سوختهای زیستی (مانند زغالچوب) بهجای کک و بهبود فرآیندهای احیا برای کاهش انتشار کربن منواکسید.
ویژگیها / معیارها | فناوری سنتی | فناوری مدرن (پیشرفته) |
---|---|---|
نوع کوره | کوره قوس الکتریکی ساده | کوره قوس با کنترل PLC و اتوماسیون کامل |
کنترل دما و ترکیب | دستی یا نیمهخودکار | دقیق و تمامخودکار با مانیتورینگ لحظهای |
مصرف انرژی الکتریکی | بالا (تا 9000 کیلوواتساعت/تن) | بهینهشده (تا 6500 کیلوواتساعت/تن) |
مصرف مواد اولیه | نرخ پرت بالا | کاهش پرت مواد با تنظیمات دقیق |
درصد خلوص سیلیسیم | متغیر (40–65%) | یکنواخت و بالا (70–90%) |
کیفیت محصول نهایی | نوسان دارد | پایدار، با استاندارد صادراتی |
آلایندگی محیط زیست | بالا (گاز و گرد و غبار) | کاهش آلایندگی با فیلترهای صنعتی پیشرفته |
قابلیت ردیابی و گزارشگیری | محدود | کامل با نرمافزارهای مانیتورینگ صنعتی |
سرعت تولید و بازدهی | پایینتر | بالاتر و مقرونبهصرفه |
هزینه نگهداری و اپراتوری | متوسط | در ابتدا بالاتر، ولی با صرفهجویی در بلندمدت |
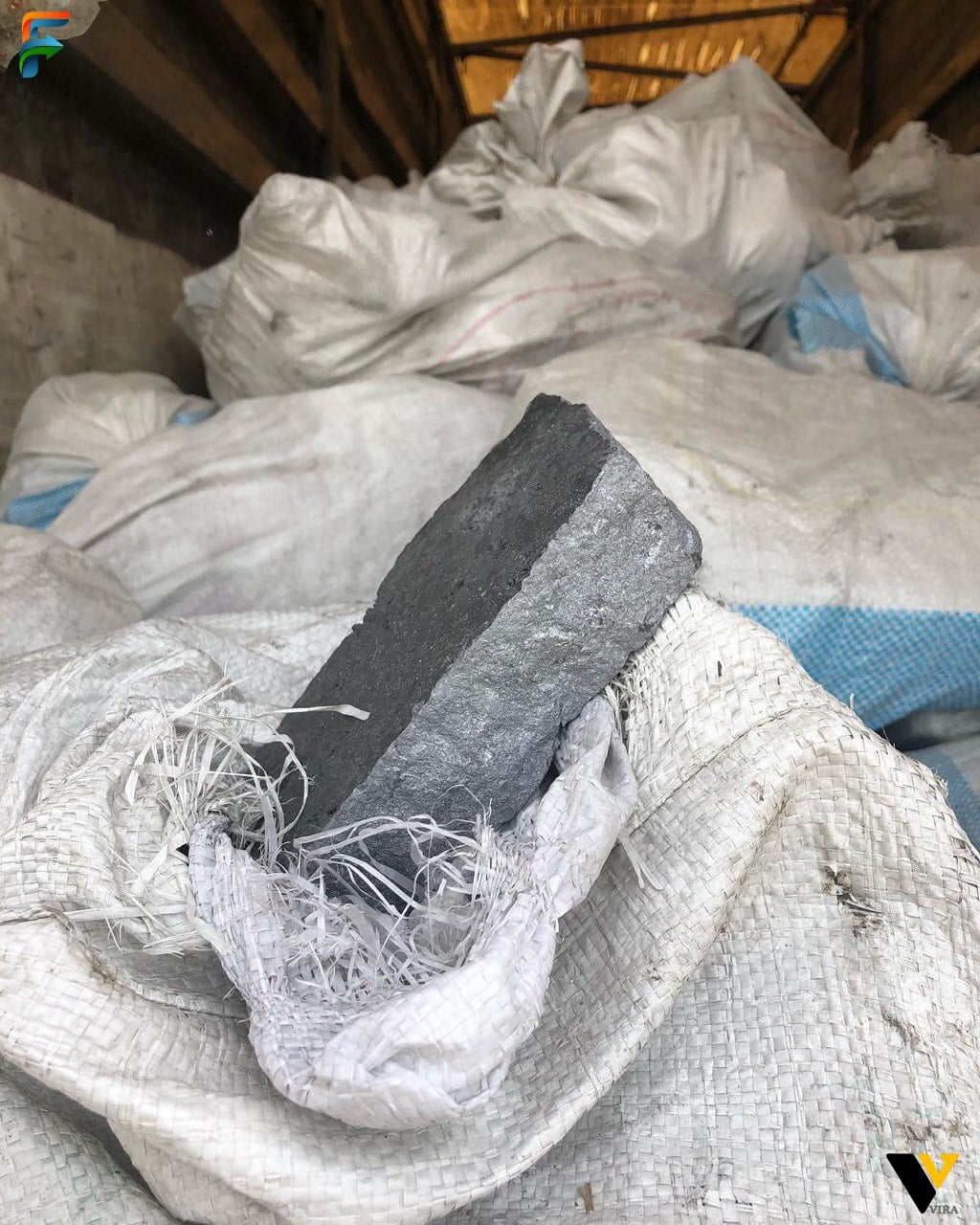
سوالات متداول درباره تولید فروسیلیس
فروسیلیس در فولادسازی (اکسیژنزدایی و افزایش استحکام)، ریختهگری چدن (جوانهزایی)، تولید منیزیم، الکترودهای جوشکاری، فولادهای مغناطیسی و صنایع شیمیایی کاربرد دارد.
این کورهها دمای بالا (تا ۲۵۰۰ درجه سانتیگراد) و شرایط کنترلشدهای برای احیای سیلیس و آهن فراهم میکنند، که برای تولید فروسیلیس با خلوص بالا ضروری است.
گریدها بر اساس درصد سیلیسیم (۱۵، ۴۵، ۶۵، ۷۵، ۹۰٪) و میزان ناخالصیها (مانند آلومینیوم و کربن) طبقهبندی میشوند. گریدهای با سیلیسیم بالا برای کاربردهای تخصصی و گریدهای استاندارد برای مصارف عمومی مناسباند.
با استفاده از سیستمهای فیلتراسیون مدرن و بازیافت غبار میکروسیلیکا، آلودگی به حداقل رسیده است. بااینحال، انتشار گازهای گلخانهای همچنان نیاز به مدیریت دارد.
کنترل کیفیت مواد اولیه، نظارت بر نسبتهای شارژ، استفاده از سیستمهای اتوماسیون و آنالیز شیمیایی محصول نهایی در آزمایشگاههای مجهز، کیفیت را تضمین میکند.
نتیجهگیری: فروسیلیس، ستون صنعت مدرن
فروسیلیس به عنوان یکی از مهمترین فروآلیاژها، نقشی بیبدیل در توسعه صنایع متالورژی و فولادسازی ایفا میکند.
فرآیند تولید آن، که ترکیبی از علم شیمی، مهندسی مواد و تکنولوژی پیشرفته است، با چالشهایی مانند مصرف بالای انرژی و مسائل زیستمحیطی همراه است، اما پیشرفتهای اخیر در اتوماسیون، بازیافت و بهینهسازی انرژی، این صنعت را به سمت پایداری و کارایی بیشتر سوق داده است. 🔄
در ایران، با وجود منابع غنی سیلیس و زیرساختهای صنعتی روبهرشد، تولید فروسیلیس نهتنها نیاز داخلی را تأمین میکند، بلکه فرصتهای صادراتی قابلتوجهی به بازارهای منطقهای و جهانی ارائه میدهد.
با توجه به هدفگذاری تولید ۵۵ میلیون تن فولاد تا سال ۱۴۰۴، تقاضا برای فروسیلیس بهطور پیوسته افزایش خواهد یافت، که این امر ضرورت سرمایهگذاری در فناوریهای جدید و بهبود فرآیندها را برجسته میکند.
در آینده، تمرکز بر فناوریهای سبز، کاهش انتشار کربن و توسعه محصولات با ارزش افزوده بالا، میتواند جایگاه فروسیلیس را در زنجیره تأمین جهانی تقویت کند. 🌟
در پایان، تولید فروسیلیس نهتنها یک فرآیند صنعتی، بلکه نمادی از تلفیق دانش، نوآوری و تلاش برای خلق موادی است که پایه تمدن صنعتی مدرن را تشکیل میدهند.